Spherical Plain Bearing 0E6B0149
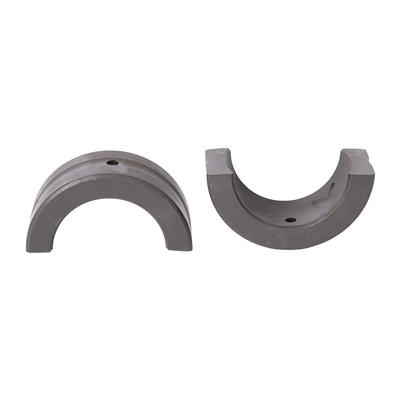
The sensor means is a Hall effect sensor that comprises a strip magnet 86 with north and south poles aligned along its length. It is bonded to a metal strip 88, which is bolted to the shock body 26. The metal strip serves as a protective shield and prevents the magnetic strip 86 from becoming exposed to adverse environments.The semi-active shock absorber is controlled by a control system, which is composed of circuit boards, A/D/A converters, and memory chips. The control system determines the damping level of the shock absorber assembly 20, which changes as a function of the fluid flow. Depending on the type of control system used, the damping level can be changed on a millisecond basis.Another approach is to use frequency-dependent damping. This type of damping is more environmentally friendly than conventional mechanisms because it does not use any oil.
This method also provides more consistent damping performance over a wide range of temperatures. Another technique is called Micro-Amplitude Damping (MAD), which uses a position-sensitive hydraulic circuit to react to the displacement of the shock absorber.Lightweight materials for automotive suspension parts are made from a variety of materials and can be used to help cars reduce their weight. These materials include composites made of epoxy resin and vinylester resin with steel inserts. These materials can reduce the weight of a car's suspension by up to 35% and are especially suitable for high-volume production.The growth of the automotive lightweight materials market is expected to accelerate in the coming years as more car manufacturers look to lower their vehicle's weight and increase fuel efficiency.
Several factors are driving the market for automotive lightweight materials, including stringent vehicle emission regulations and government initiatives to reduce CO2 emissions.The increased popularity of electric vehicles is expected to continue to fuel the market for automotive lightweight materials. The Economist Intelligence Unit estimates that sales of electric vehicles will rise from 2.5 million in 2020 to more than 3.4 million by 2021. According to CNBC, the production of electric vehicles will reach 1.3 million this year and may reach 1.5 million in 2021, depending on market conditions. As the market for automotive lightweight materials grows, manufacturers will have to increase their production rates to meet these new vehicle regulations.